Solve the problem of forgetting to tighten bolts and screws once and for all
When automatically tightening bolts and screws, you don't have to worry about forgetting to tighten them.
But for work that cannot be automated, they must be tightened by a person, and in such cases, human error inevitably occurs.
Forgetting to tighten bolts and screws is one of the most common human errors.
Adrec products can solve the problem of forgetting to tighten bolts and screws.
Here are countermeasures against common causes of forgetting to tighten, using our products.
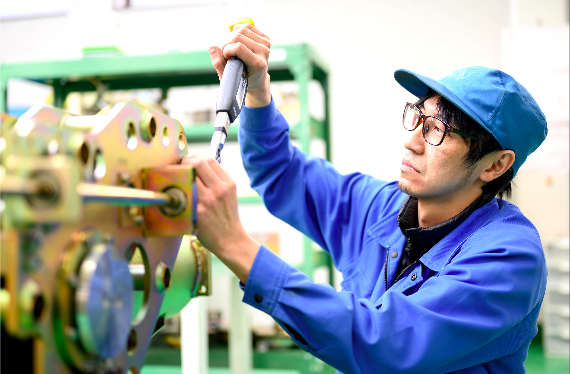
Quality defects caused by forgetting to tighten bolts and screws
There have been cases where insufficient torque has caused automobile and heavy vehicle tire nuts to drop off while driving, resulting in loss of control.
Insufficient screw torque causes the screws to loosen which in turn causes parts to come loose from each other when exposed to repeated thermal contraction caused by vibration and temperature changes.
Therefore, if the applied torque is less than specified, the risk of parts falling off and causing failure during operation increases.
Causes of forgetting to tighten bolts and screws
Cause | Details |
Not tightening the bolts while they are temporarily tightened. | Cases where bolts are only temporarily tightened and slip by out without being fully tightened. |
Overcounting due to retightening | Cases where, even though the tightening count is controlled, there are bolts and screws that have already been tightened are re-tightened and those that slip by out without being tightened. |
Confirmation errors due to work stoppages | Cases where interruptions occur, such as being spoken to in the middle of work, and mistakes are made. |
Commonly taken measures to prevent forgetting to tighten
Cause | Measures |
Not tightening the bolts while they are temporarily tightened. | When the final tightening is completed, a "match mark" is applied with a magic marker. Confirmation of retightening by a third-party check |
Overcounting due to retightening | Confirmation of retightening by a third-party check |
Confirmation errors due to work stoppages | Do not talk or distract others, and leave identification cards in place if it becomes necessary to abruptly stop and leave the site. Confirmation of retightening by a third-party check |
The more measures taken, the lower the production efficiency.
Any of these measures involve work that must be done in addition to the original tightening work.
The more mistakes occur, the more confirmation work is required, and production efficiency declines rapidly.
Prevents forgetting to tighten and improves production efficiency,
Introducing Adrec's digital wrench "ProWrench"
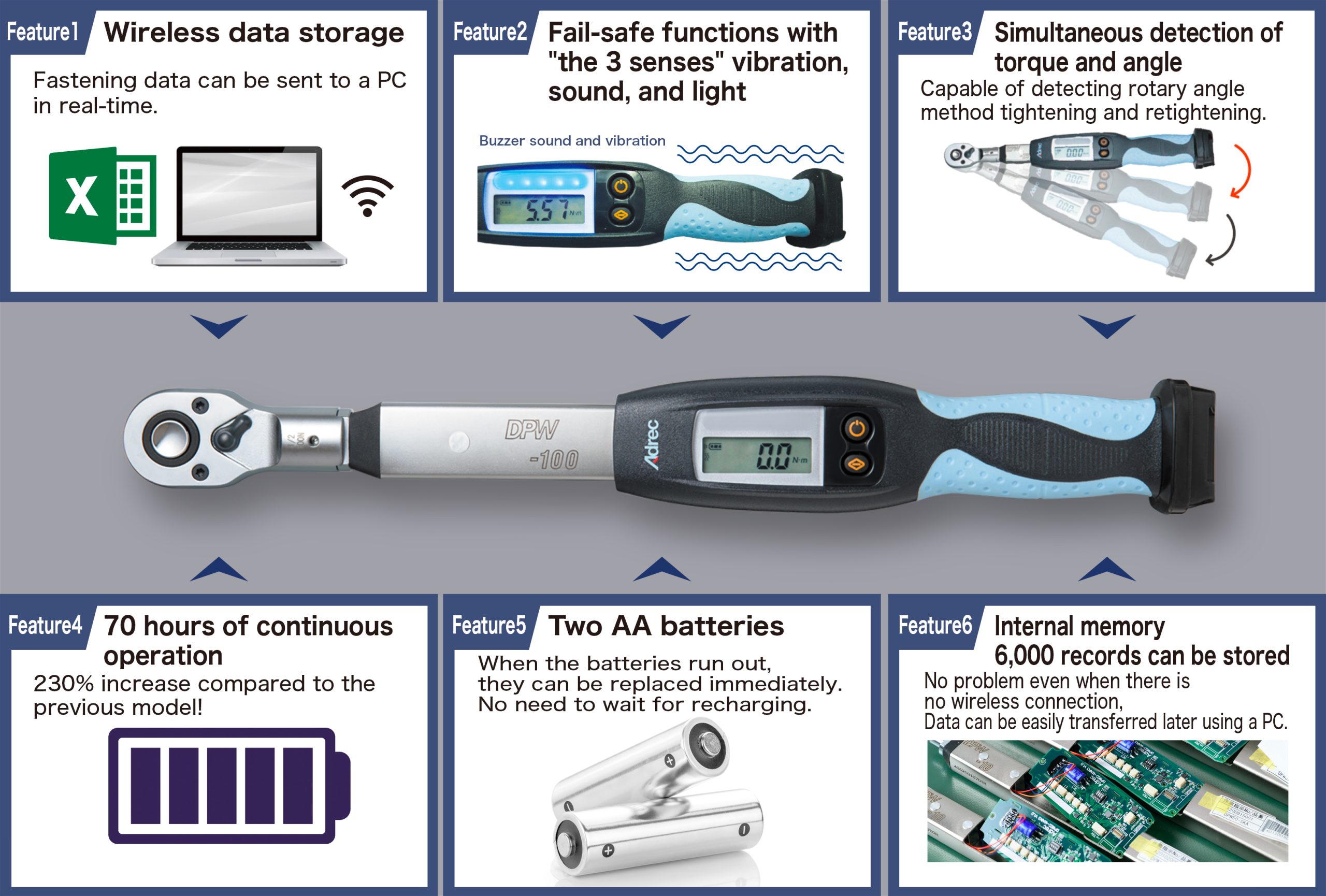
1. Tightening pattern registration
The ProWrench can have 10 different tightening pattern settings. The settings include lower and upper limit torque, number of tightening control cycles, among others.
It is also possible to create settings for temporary tightening and final tightening in advance, and switch the settings manually when working, or to set up a destination pattern to automatically change the settings when a predetermined number of cycles has been reached.
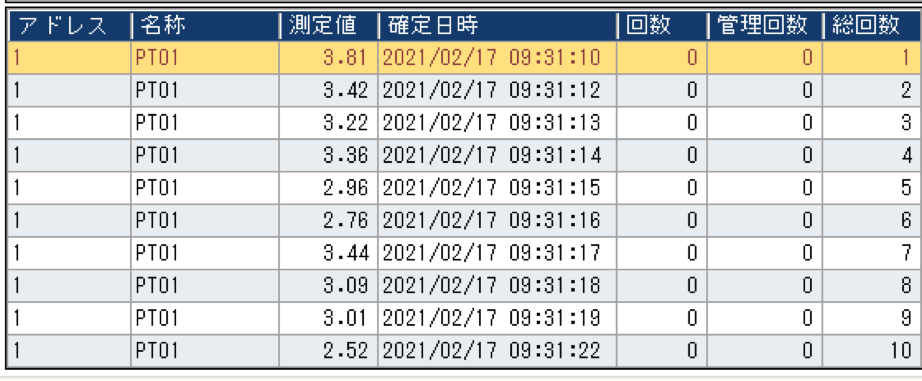
2. Retightening prevention function
But, if pattern registration is used by itself, won't the tightening of screws and bolts that have already been tightened be counted as cycles?
In such cases, the retightening prevention function can be used to prevent this.
If, during tightening work, a screw or bolt does not rotate more than a specified angle, the operator is notified with vibration and warning sounds and the number of control cycles will not be counted up. If an already tightened screw or bolt is re-tightened by accident, it wont rotate very much, allowing detection of this fail-safe mistake.
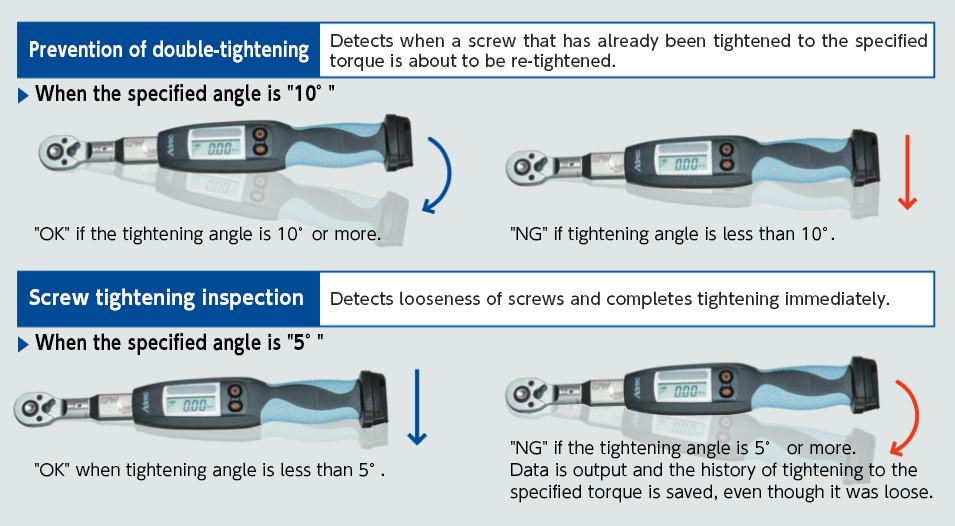
3. Manufacturing support software - Automatic setup with DigiProMaster
But, even if the number of cycles is correct, is it possible have accidentally switched to the wrong pattern setting?
If you use DigiProMaster, it can automatically switch the set torque values for each process, so workers do not have to switch settings manually.
If multiple torque wrenches are used, there's no problem if the wrong torque wrench is secleted, thereby preventing fail-safe mistakes. If the number of tightening cycles is not reached with the torque wrench that is being used, the operator cannot proceed to the next step, so they can work without having to worry about such problems.
*Retighening prevention function is also supported.

4. Work instructions linked to the display
If work gets interrupted, could the worker forget to finish tightening?
If they work with a DigiProMaster, they can finish the temporary tightening and stop the work before the main tightening work.
When work resumes, the tightening process will start from the main tightening, so there will be no forgetting to tighten.
Although this should not happen, if work is interrupted after only two out of four tightenings, the status of the work is displayed on the screen so that the operator can see where to resume work.
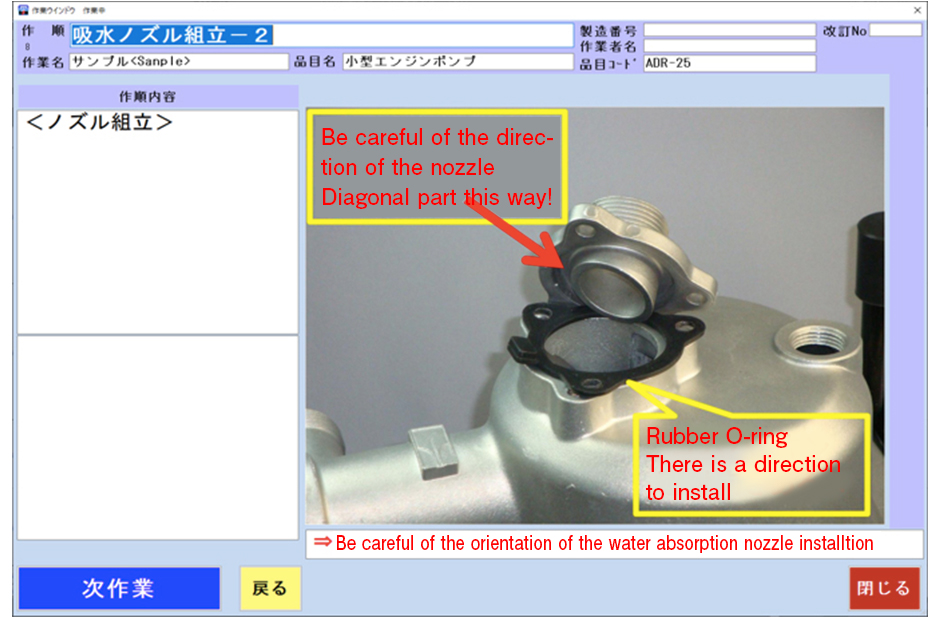
5. In-house manufacturing support software
We developed our own in-house manufacturing support software. Can we send and receive data between our software and ProWrench?
You can use the class libraries that are provided free of charge, so it is possible to easily configure the ProWrench and receive tightening data that way.
If the in-house software counts the number of times it receives normal tightening data and takes measures to prevent mistakes such as forgetting to tighten, then operators can concentrate on their work with peace of mind.
With knowledge of VBA, it is also possible to perform ProWrench operations and receive tightening data using Excel.
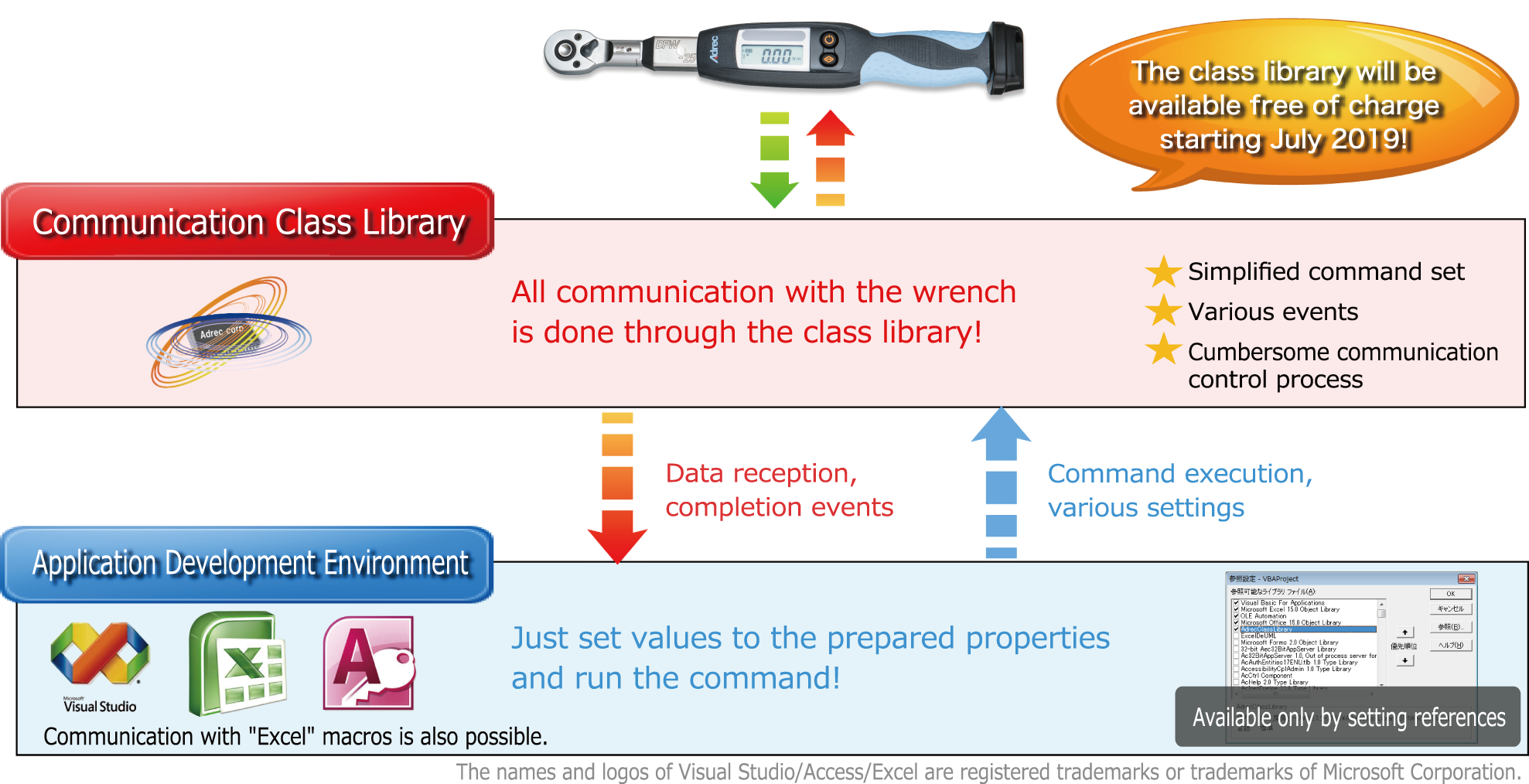
6. Linking with PLCs
Do you support using PLCs to carry out manufacturing support instead of Windows?
Since the communication format is disclosed, if the customer sets up their own ladder logic, it would be possible to build a PLC-linked system that prevents mistakes such as forgetting to tighten. The system would have to be built from scratch by the customer though.

Linking with machine tools
Link to machine tools using a PLC (sequencer).
Customers who are considering purchasing
Many companies have already adopted our products and are using them in a wide variety of ways.
Please contact us first and we will create the optimal proposal for your company.
Online consultations are also available.
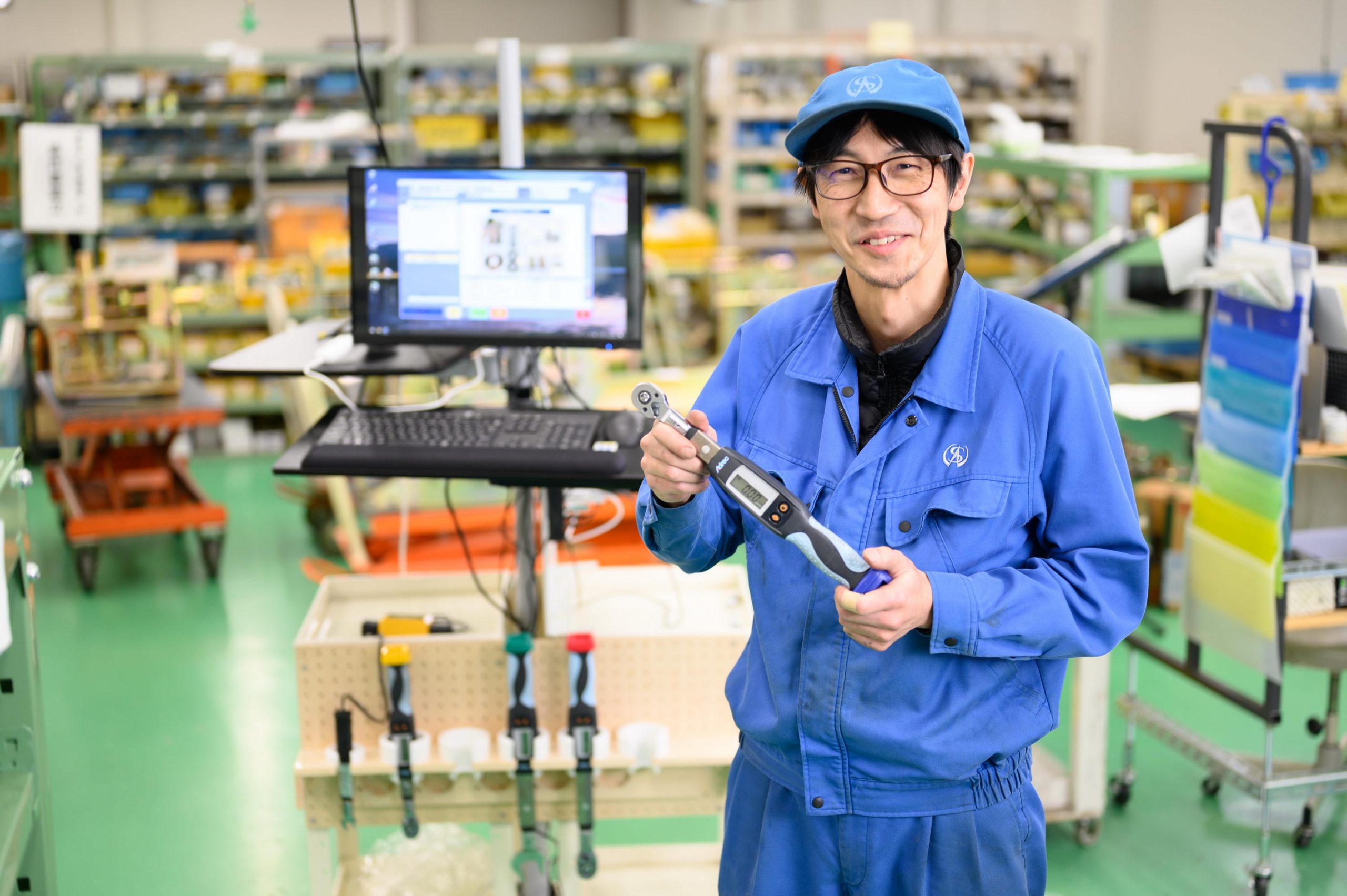